Success Stories
From The Leader in Clean Power Production Technologies
Edmonton, Alberta, Canada Success Story
Unique Construction Approach to Refinery Boiler Refurbishment
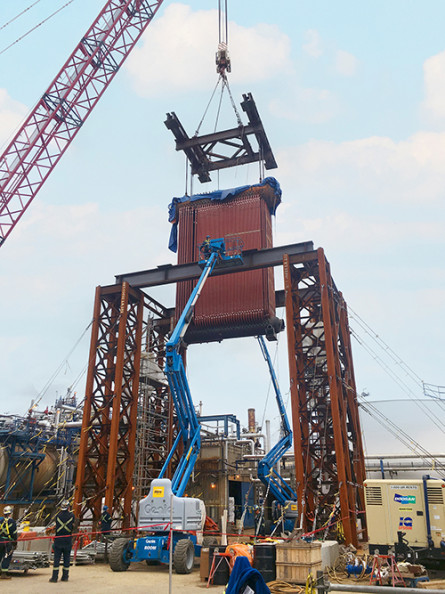
B&W’s construction team built the replacement boiler in a jig concurrent with the demolition of the existing unit to minimize the plant’s outage time.
Background
An oil refinery in Edmonton, Alberta, Canada was experiencing boiler failures that were having a frequent and negative impact on its operations. The unit, a competitor’s natural gas-fired boiler designed to produce 250,000 lb/hr of superheated steam, was used by the refinery for both power and process applications, but it had reached the end of its useful life. During failures, the plant would either operate at lowered production levels or purchase excess steam from a neighboring plant at a premium.
The customer needed a cost-effective solution that:
- Provided consistently reliable power production
- Adhered to an accelerated project execution schedule to minimize production losses
B&W Advantage
The customer was familiar with the value Babcock & Wilcox (B&W) brought to projects from past work we had performed for them. This experience demonstrating our quality and trust earned our consideration, but it was our plan and full-scope capabilities for this specific challenge that resulted in our award of the work. Our ability to provide comprehensive engineering, materials and construction services reduced complexity and risk, and streamlined accountability, communication and project management.
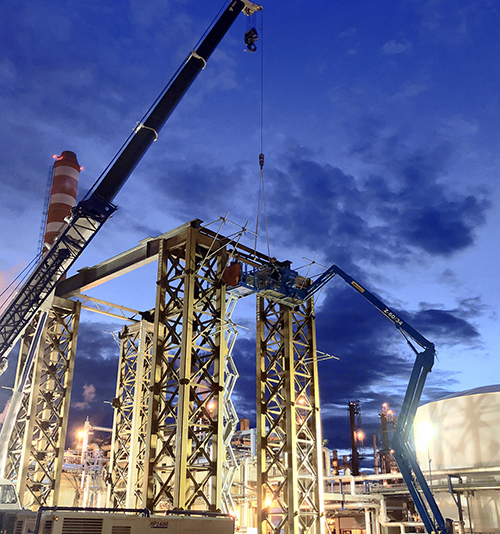
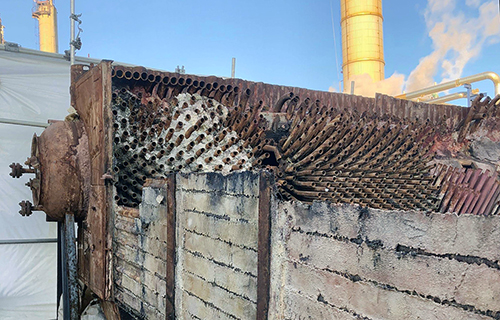
The construction team disassembled the existing unit that was negatively impacting the plant’s production.
Scope of Supply
The existing unit needed to be overhauled, requiring expertise from across B&W:
- Engineering and supply scope included replacing 100% of the boiler’s pressure parts, including steam and lower drums, generating bank, superheater, furnace and other miscellaneous equipment supply
- Construction scope included onsite mechanical erection of the boiler, working in parallel and collaborating with crane, scaffold, insulation and other service providers
Boiler Replacement
B&W proposed a boiler that was nearly identical to the existing boiler. When running properly, the existing boiler’s design met the plant’s needs, and by providing a direct replacement, the plant was able to maintain its existing emissions permit. This avoided delays as well as additional scope and costs that would have been required with a new emissions permit.
Results
Utilizing the former boiler’s design to eliminate the need for a new emissions permit, coupled with the innovative jig construction approach, made for a fast-tracked and financially viable solution. The project was executed successfully and met all guarantees. The contract was awarded mid-2018, and the plant was back online making steam by October 2019. This project showcases how the linkage of creative engineering, material supply and advanced construction planning come together to meet ambitious goals and minimize impacts to customer operations during and well after project completion.
Unique Approach
The replacement boiler was too large to ship in a single piece and would need to be built onsite. Typical construction plans would have called for the demolition of the former boiler and then building the new one in its place. Instead, we erected the new boiler in a construction jig so that decommissioning the old and constructing the new could be done concurrently. By performing these activities simultaneously, the scheduled outage time was reduced by nearly 50 percent.